In March 2020, the UK’s manufacturing sector was tasked with its biggest challenge of a generation; to address the terrifying prospect of a huge shortfall in ventilators in the UK, in response to the overwhelming impact of the Covid-19 pandemic.
The response to the challenge is nothing short of inspirational. The story of collaboration and collective effort, combined with creative thinking and embracing new technologies and new ways of working is incredible. And one of the keys to success was the adoption of mixed reality to inform both design and production processes, in addition to its critical role in addressing the epic challenge of training thousands of workers to produce new products at a seemingly impossible scale.
Collaboration was key to rise to the challenge
The call to UK manufacturers was a monumental ask; to produce at least 20 years-worth of ventilators in 12 weeks. As if this wasn’t challenging enough, many of the manufacturers and engineering businesses tasked with production had never produced ventilators before.
The collaborative response to the Ventilator Challenge was one of the greatest feats ever witnessed in the history of UK manufacturing. Traditional rivalries were set aside as a consortium of aerospace, motorsport, automotive and medical businesses including all UK-based Formula 1 car manufacturers, Ford, GKN Aerospace, Airbus, Meggitt and Siemens UK came together to work towards one common goal.
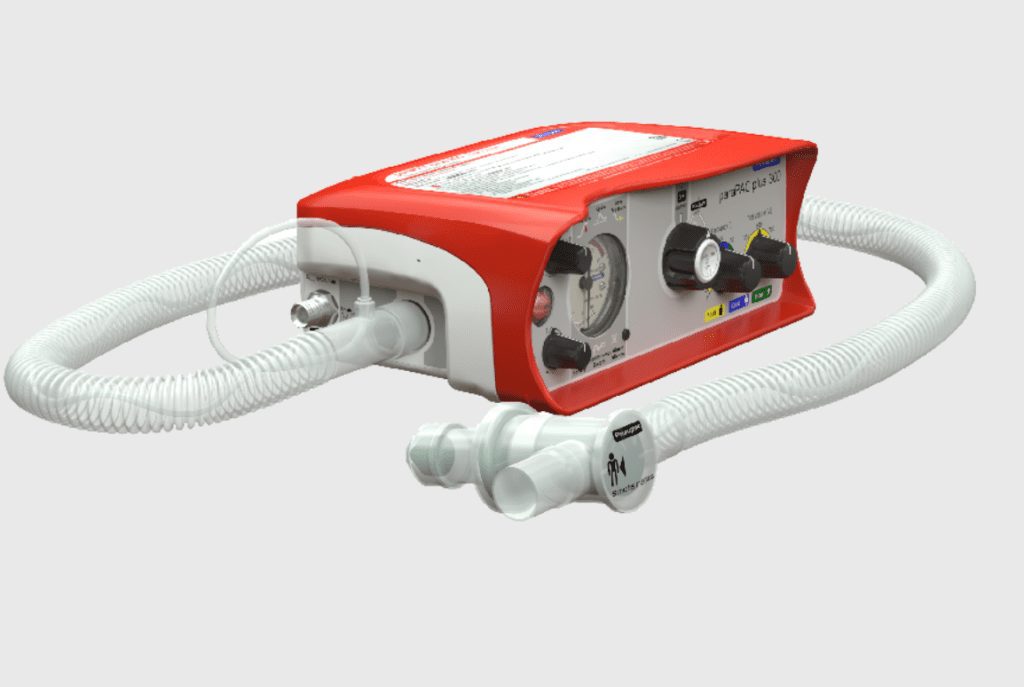
The consortium was split into two different programmes to produce two types of ventilators. The Smith paraPAC plus™ was an already tried and tested model, however the Penlon model was a concept based on modifying existing clinical equipment, so required the added challenge of rapidly design and testing to meet regulatory approval. Additionally, seven new large-scale factories were set up across the UK, as well as restructuring the existing Smiths Medical site in Luton and Penlon in Abingdon to cope with the demands of production.
Immersive technology: a crucial part of the design and production jigsaw
“By using the power of augmented reality, we have reduced set-up lead times and developed a manufacturing approach that will help the consortium scale up from 50 to 60 ventilators combined capacity per week to produce at least 1,500 units of the Penlon and Smiths models every seven days.”
Paul Haimes, vice president of field engineering at PTC
Immersive technologies provided a crucial part of collaborative efforts throughout the design and production of ventilators across multiple sites, from the development of a digital twin of the production sites at the start of the process through to training over 3,500 employees in total. In the case of the Penlon model, this also included learning how to produce a totally new product with 812 assembly parts.
PTC’s Vuforia Expert Capture AR technology and Microsoft’s HoloLens were used to capture each of the assembly steps and all processes involved in building the ventilators. This fed into speedy development of new design iterations of the ventilator, in addition to feeding into a comprehensive virtual training manual to ensure that the production workforce was trained effectively.
Benefits of using immersive tech
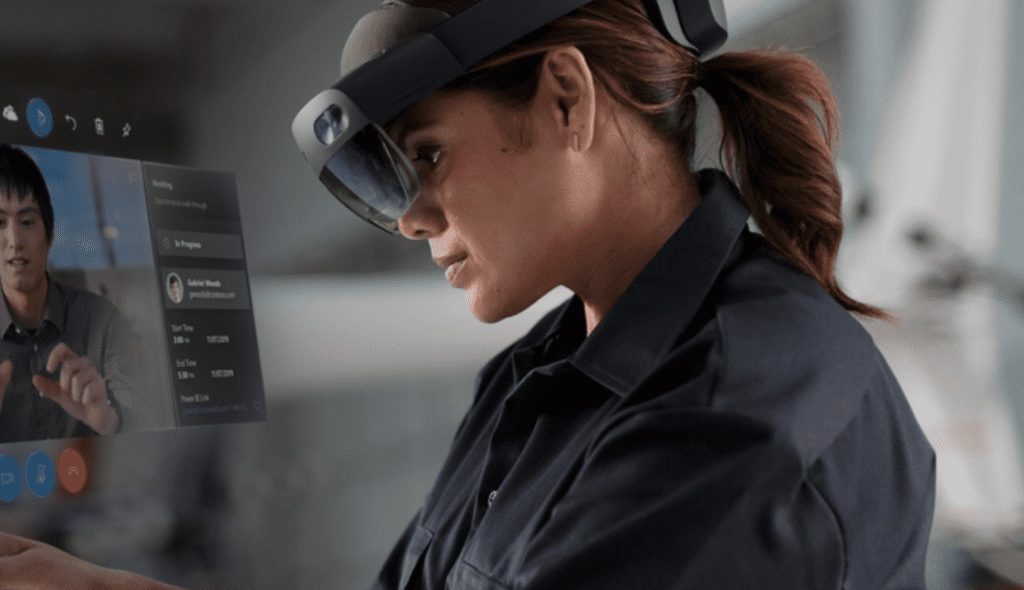
“Microsoft’s mixed reality headset has been used to capture the highly specialised ventilator production process to train and upskill the consortium’s new workforce in multiple manufacturing sites across the UK – many of whom have been brought in overnight and are used to manufacturing aerospace and automobile parts. A step by step guide has been added to training footage captured on HoloLens 2 for workers to use across the country as they build replica assembly lines from scratch and begin production.”
Dick Elsy, CEO, High Value Manufacturing Catapult
In terms of training, the Ventilator Challenge highlights the power of immersive tech to rapidly train a workforce at scale, and speed up the production process through improving knowledge retention and minimising errors.
Key benefits:
- Take an agile approach to developing effective training guides
Speed was of the essence in the development and production of ventilators and immersive technology was used as part of the design process through capturing every stage of the build process using Vuforia. This enabled the consortium to rapidly interrogate systems and learn where improvements, which then fed into informing both design development and the practical rollout. This captured learning was helped to rapidly create immersive training guides that could be shared across the consortium to ensure consistency and quality of production across multiple sites.
- Rapidly train thousands
The Ventilator Challenge offers an extreme example of how immersive technologies are ideally designed to support effective and efficient learning – and highlight how the tech allows training to be easily scaled up, as well as out across numerous environments. In practical terms, over 80 Hololens 2 devices were shared amongst multiple factory sites to help train over 3,500 people over a period of weeks. At Ford alone, the sub-assembly plant inducted over 850 people and completed over 18,000 hours of training (this would usually equate to usually over two years of training) in just seven weeks.
- Speed up production by learning on the job
Crucially, as mixed reality blurs the lines between the real and virtual space, Microsoft’s Brandy Moore highlights that the rate of knowledge retention is 80% higher when learning on the job with the aid of a Hololens, rather than using a printed user guide. Immersive technologies allow workers to learn by doing, which has the dual benefit of speeding up training and improving retention of knowledge, whilst minimising production downtime, as workers are able to continue to contribute to production while they receive thorough training and ongoing tailored support.
- Minimise risk for people working in the production sites
Another benefit of embracing immersive technologies throughout the process was that developers could work remotely, as well as ensuring that the number of people on the production floor was limited. Given the need for social distancing during lockdown, bringing in experts to train staff across multiple sites could have put thousands of people’s health at risk unnecessarily; by supporting remote communications and bringing expert knowledge to the factory floor through the use of augmented reality, this risk was significantly minimised.
A blueprint for future training in manufacturing… and beyond?
The response to the UK’s Ventilator Challenge was an incredible feat of manufacturing that succeeded through unprecedented collaboration, the sharing of expertise and knowledge and harnessing the power of technology effectively; including immersive technology. And although it is a unique project in response to extraordinary circumstances, it highlights how immersive technologies can be embraced by the manufacturing sector – and beyond, to customise training on a mass scale to improve and streamline processes.
To find out more about how Future Visual can help to introduce immersive technology solutions into your company, contact us at https://www.futurevisual.com/visionxr/
Further reading/viewing
- Hear directly from the teams involved. Watch the Microsoft Hololens and the UK Ventilator Challenge webinar from Immerse UK
- Hear more about the Challenge directly from PTC and about how Vuforia was central to the project
- Read more from Microsoft about how Hololens 2 was deployed
In March 2020, the UK’s manufacturing sector was tasked with its biggest challenge of a generation; to address the terrifying prospect of a huge shortfall in ventilators in the UK, in response to the overwhelming impact of the Covid-19 pandemic.
The response to the challenge is nothing short of inspirational. The story of collaboration and collective effort, combined with creative thinking and embracing new technologies and new ways of working is incredible. And one of the keys to success was the adoption of mixed reality to inform both design and production processes, in addition to its critical role in addressing the epic challenge of training thousands of workers to produce new products at a seemingly impossible scale.
Collaboration was key to rise to the challenge
The call to UK manufacturers was a monumental ask; to produce at least 20 years-worth of ventilators in 12 weeks. As if this wasn’t challenging enough, many of the manufacturers and engineering businesses tasked with production had never produced ventilators before.
The collaborative response to the Ventilator Challenge was one of the greatest feats ever witnessed in the history of UK manufacturing. Traditional rivalries were set aside as a consortium of aerospace, motorsport, automotive and medical businesses including all UK-based Formula 1 car manufacturers, Ford, GKN Aerospace, Airbus, Meggitt and Siemens UK came together to work towards one common goal.
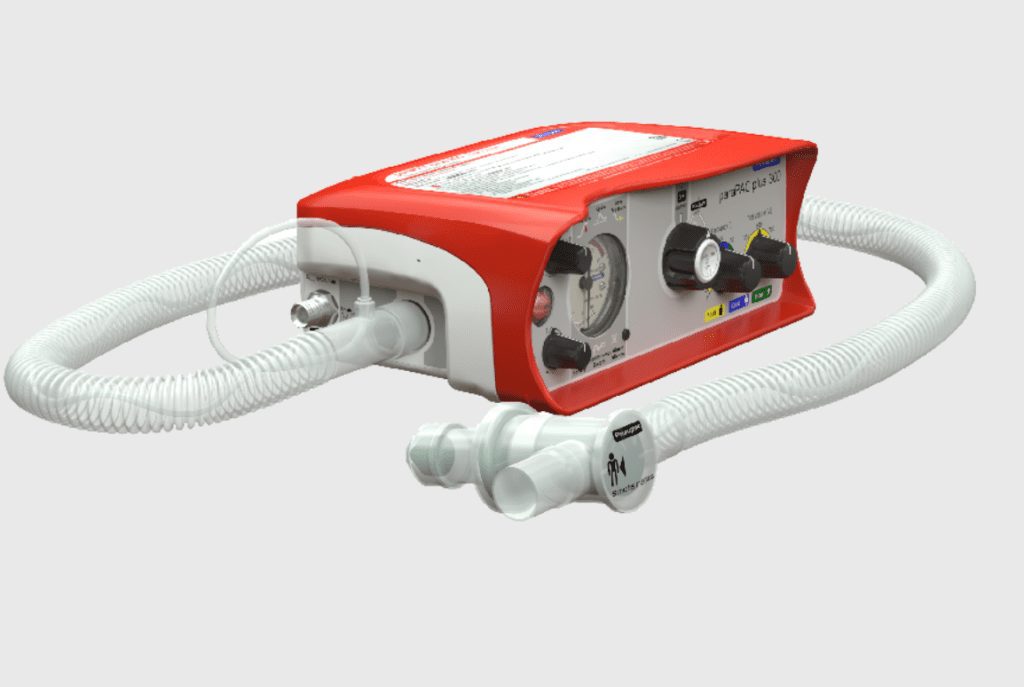
The consortium was split into two different programmes to produce two types of ventilators. The Smith paraPAC plus™ was an already tried and tested model, however the Penlon model was a concept based on modifying existing clinical equipment, so required the added challenge of rapidly design and testing to meet regulatory approval. Additionally, seven new large-scale factories were set up across the UK, as well as restructuring the existing Smiths Medical site in Luton and Penlon in Abingdon to cope with the demands of production.
Immersive technology: a crucial part of the design and production jigsaw
“By using the power of augmented reality, we have reduced set-up lead times and developed a manufacturing approach that will help the consortium scale up from 50 to 60 ventilators combined capacity per week to produce at least 1,500 units of the Penlon and Smiths models every seven days.”
Paul Haimes, vice president of field engineering at PTC
Immersive technologies provided a crucial part of collaborative efforts throughout the design and production of ventilators across multiple sites, from the development of a digital twin of the production sites at the start of the process through to training over 3,500 employees in total. In the case of the Penlon model, this also included learning how to produce a totally new product with 812 assembly parts.
PTC’s Vuforia Expert Capture AR technology and Microsoft’s HoloLens were used to capture each of the assembly steps and all processes involved in building the ventilators. This fed into speedy development of new design iterations of the ventilator, in addition to feeding into a comprehensive virtual training manual to ensure that the production workforce was trained effectively.
Benefits of using immersive tech
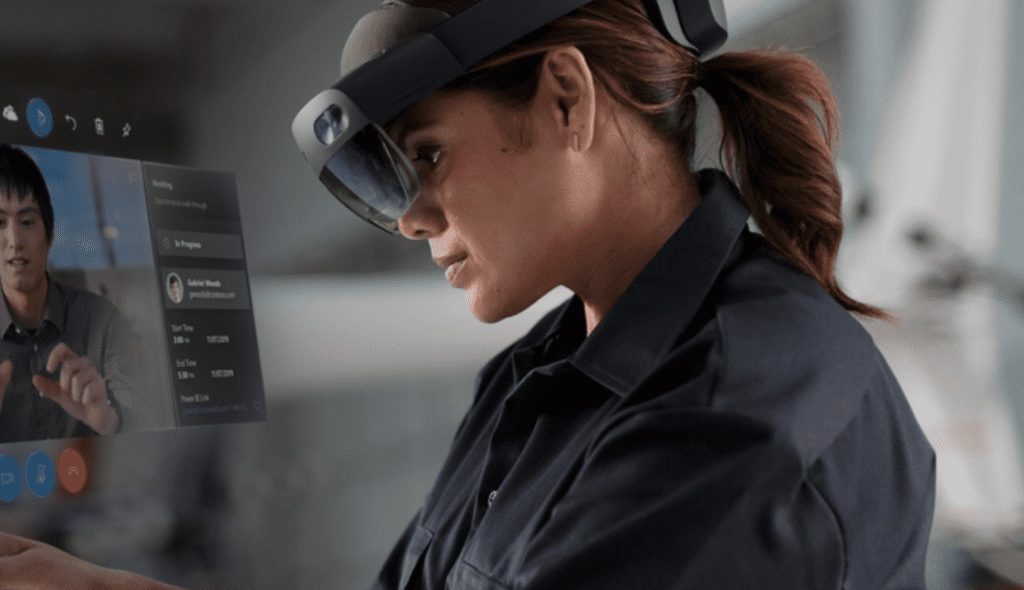
“Microsoft’s mixed reality headset has been used to capture the highly specialised ventilator production process to train and upskill the consortium’s new workforce in multiple manufacturing sites across the UK – many of whom have been brought in overnight and are used to manufacturing aerospace and automobile parts. A step by step guide has been added to training footage captured on HoloLens 2 for workers to use across the country as they build replica assembly lines from scratch and begin production.”
Dick Elsy, CEO, High Value Manufacturing Catapult
In terms of training, the Ventilator Challenge highlights the power of immersive tech to rapidly train a workforce at scale, and speed up the production process through improving knowledge retention and minimising errors.
Key benefits:
- Take an agile approach to developing effective training guides
Speed was of the essence in the development and production of ventilators and immersive technology was used as part of the design process through capturing every stage of the build process using Vuforia. This enabled the consortium to rapidly interrogate systems and learn where improvements, which then fed into informing both design development and the practical rollout. This captured learning was helped to rapidly create immersive training guides that could be shared across the consortium to ensure consistency and quality of production across multiple sites.
- Rapidly train thousands
The Ventilator Challenge offers an extreme example of how immersive technologies are ideally designed to support effective and efficient learning – and highlight how the tech allows training to be easily scaled up, as well as out across numerous environments. In practical terms, over 80 Hololens 2 devices were shared amongst multiple factory sites to help train over 3,500 people over a period of weeks. At Ford alone, the sub-assembly plant inducted over 850 people and completed over 18,000 hours of training (this would usually equate to usually over two years of training) in just seven weeks.
- Speed up production by learning on the job
Crucially, as mixed reality blurs the lines between the real and virtual space, Microsoft’s Brandy Moore highlights that the rate of knowledge retention is 80% higher when learning on the job with the aid of a Hololens, rather than using a printed user guide. Immersive technologies allow workers to learn by doing, which has the dual benefit of speeding up training and improving retention of knowledge, whilst minimising production downtime, as workers are able to continue to contribute to production while they receive thorough training and ongoing tailored support.
- Minimise risk for people working in the production sites
Another benefit of embracing immersive technologies throughout the process was that developers could work remotely, as well as ensuring that the number of people on the production floor was limited. Given the need for social distancing during lockdown, bringing in experts to train staff across multiple sites could have put thousands of people’s health at risk unnecessarily; by supporting remote communications and bringing expert knowledge to the factory floor through the use of augmented reality, this risk was significantly minimised.
A blueprint for future training in manufacturing… and beyond?
The response to the UK’s Ventilator Challenge was an incredible feat of manufacturing that succeeded through unprecedented collaboration, the sharing of expertise and knowledge and harnessing the power of technology effectively; including immersive technology. And although it is a unique project in response to extraordinary circumstances, it highlights how immersive technologies can be embraced by the manufacturing sector – and beyond, to customise training on a mass scale to improve and streamline processes.
To find out more about how Future Visual can help to introduce immersive technology solutions into your company, contact us at https://www.futurevisual.com/visionxr/
Further reading/viewing
- Hear directly from the teams involved. Watch the Microsoft Hololens and the UK Ventilator Challenge webinar from Immerse UK
- Hear more about the Challenge directly from PTC and about how Vuforia was central to the project
- Read more from Microsoft about how Hololens 2 was deployed